How you can check pace sensor? This information breaks down the whole lot it’s worthwhile to know, from the fundamentals of sensor varieties to superior troubleshooting. Get able to degree up your pace sensor recreation! We’ll cowl widespread varieties, testing strategies, and even some cool case research. Bali vibes, tech expertise, multi functional!
Velocity sensors are essential in numerous fields, from automotive to industrial automation. Understanding methods to precisely check them is vital for optimum efficiency and avoiding expensive downtime. This detailed information will equip you with the data to confidently assess the well being and performance of your pace sensors.
Introduction to Velocity Sensors
Velocity sensors are essential elements in numerous functions, enabling exact measurement and management of pace. They play an important position in industries starting from automotive and aerospace to manufacturing and robotics. Understanding the differing types and their operational ideas is important for choosing the suitable sensor for a selected job.Velocity sensors are gadgets that measure the rotational pace or linear velocity of a transferring object.
They arrive in numerous varieties, every using a novel methodology to find out the pace. The selection of sensor is dependent upon elements such because the surroundings, the pace vary to be measured, and the required accuracy.
Widespread Sorts of Velocity Sensors
Various kinds of pace sensors make the most of numerous bodily ideas to find out pace. These strategies are tailored to particular necessities of the appliance, such because the working surroundings, pace vary, and precision calls for. Choosing the proper kind is essential for dependable operation.
Optical Velocity Sensors
Optical pace sensors use gentle beams to detect the motion of an object. A typical implementation entails a light-weight supply, a photodetector, and a rotating disc or encoder. As the article rotates, the sunshine beam is interrupted, and the frequency of interruption corresponds to the rotational pace. This kind is usually employed in functions requiring excessive accuracy and reliability, equivalent to industrial automation.
Magnetic Velocity Sensors
Magnetic pace sensors make the most of the precept of magnetic fields to measure the pace. These sensors usually use a rotating magnetic discipline or a magnetic encoder to generate a sign proportional to the pace. Magnetic sensors are sometimes utilized in functions the place the surroundings is harsh or the place there’s a want for top robustness.
Ultrasonic Velocity Sensors
Ultrasonic pace sensors depend on the precept of time of flight. By emitting and receiving ultrasonic waves, the sensor measures the time taken for the wave to journey to a goal and again. The pace is calculated primarily based on this time measurement. This methodology is often used for non-contact pace measurement in numerous industrial and automotive functions.
Inductive Velocity Sensors
Inductive pace sensors function on the precept of electromagnetic induction. A rotating object with a conductive floor induces a voltage in a coil, and the frequency of this induced voltage is immediately associated to the pace of rotation. These sensors are sometimes utilized in functions the place the article being measured is metallic.
Comparability of Velocity Sensors, How you can check pace sensor
Sensor Kind | Precept of Operation | Functions | Typical Output Alerts |
---|---|---|---|
Optical | Interruption of sunshine beam | Industrial automation, robotics, automotive | Pulse trains, analog voltage |
Magnetic | Rotating magnetic discipline or encoder | Automotive, industrial equipment, robotics | Pulse trains, analog voltage |
Ultrasonic | Time of flight of ultrasonic waves | Non-contact pace measurement, industrial processes | Analog voltage, digital alerts |
Inductive | Electromagnetic induction | Metallic objects, industrial equipment | Pulse trains, analog voltage |
Testing Methodology: How To Check Velocity Sensor
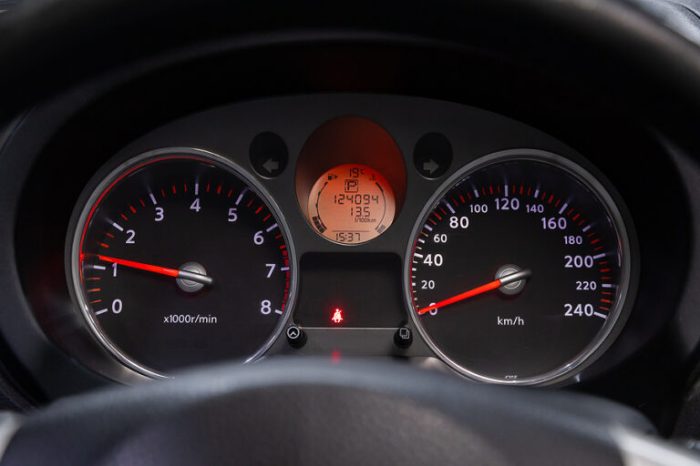
Evaluating pace sensor efficiency entails a scientific method to make sure accuracy and reliability. Thorough testing procedures are essential for figuring out potential points and guaranteeing the sensor’s suitability for its supposed software. This part particulars widespread testing strategies, obligatory gear, calibration methods, and the significance of environmental issues.
Widespread Testing Procedures
Varied procedures are employed to evaluate pace sensor efficiency. These embrace measuring the sensor’s output sign in opposition to recognized pace values, figuring out the sensor’s response time, and analyzing its linearity and accuracy over a variety of speeds. Constant testing procedures are important for acquiring dependable and comparable outcomes.
Mandatory Tools and Instruments
A variety of apparatus is required for complete pace sensor testing. This features a calibrated pace reference machine (e.g., a high-precision turntable or a calibrated wheel), an information acquisition system (with acceptable analog-to-digital converters), and a pc for information evaluation. Particular gear necessities might range primarily based on the sensor kind and the supposed software.
Strategies for Calibrating Velocity Sensors
Calibration methods are important for making certain correct pace sensor readings. A typical methodology entails utilizing a recognized pace reference to match the sensor’s output sign. This comparability permits for changes to be made to the sensor’s parameters to realize correct readings. One other methodology entails utilizing a mathematical mannequin to correlate sensor output with precise pace. The chosen calibration methodology is dependent upon the particular traits of the pace sensor.
Environmental Components
Environmental situations can considerably affect pace sensor efficiency. Temperature fluctuations, vibrations, and electromagnetic interference can have an effect on the sensor’s output, resulting in inaccurate measurements. Fastidiously controlling these elements throughout testing is essential for acquiring dependable outcomes. For instance, temperature variations would possibly trigger the sensor’s inner elements to develop or contract, affecting its accuracy.
Velocity Sensor Testing Strategies
Testing Methodology | Execs | Cons | Relevant Conditions |
---|---|---|---|
Direct Comparability | Easy, comparatively cheap, straightforward to know | Restricted accuracy if the reference normal isn’t exact, inclined to errors in measurement | Fundamental testing of pace sensor output in opposition to a recognized pace, introductory testing, or speedy prototyping |
Linearity Evaluation | Offers perception into the sensor’s response traits over a variety of speeds, revealing potential non-linearity | Requires a wider vary of pace values, extra complicated setup and evaluation | Analysis of sensor efficiency throughout a spectrum of working speeds, making certain consistency in output for various speeds, and figuring out non-linear responses. |
Response Time Measurement | Highlights the sensor’s capacity to trace adjustments in pace, essential for functions requiring speedy response | Could be affected by noise within the sign, requires exact timing measurements | Functions the place the sensor wants to reply shortly to adjustments in pace, like monitoring quickly transferring objects. |
Testing Parameters
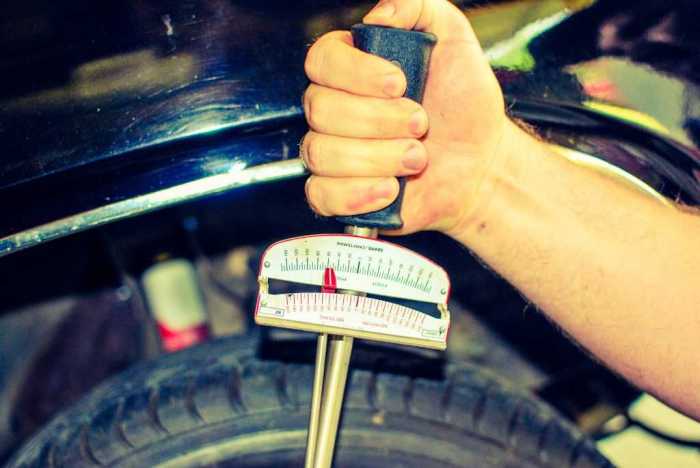
Evaluating pace sensors requires a structured method to evaluate their key efficiency indicators. Thorough testing ensures correct and dependable information acquisition. This part particulars the essential parameters to contemplate when evaluating pace sensor efficiency.
Key Efficiency Indicators (KPIs)
Understanding the important thing efficiency indicators (KPIs) is key to evaluating pace sensors. These metrics present a complete understanding of a sensor’s capabilities and limitations. Important KPIs embrace accuracy, precision, response time, linearity, noise traits, and backbone. Every KPI performs a big position in figuring out the sensor’s suitability for particular functions.
Sensor Accuracy and Precision
Accuracy and precision are elementary elements of sensor efficiency. Accuracy displays how shut a sensor’s measured worth is to the precise worth, whereas precision describes the consistency of repeated measurements. These two metrics are essential for making certain dependable information acquisition. To measure accuracy, examine the sensor’s output to a recognized normal or reference. Precision is set by repeating measurements below equivalent situations and calculating the usual deviation or variance of the outcomes.
Sensor Response Time
The response time of a pace sensor is essential for real-time functions. It measures the time it takes for the sensor to output a secure studying after a change in pace. Sensors with quicker response occasions present extra correct real-time information, which is essential in functions requiring speedy changes. Response time is measured by introducing a step change in pace and observing the time it takes for the sensor’s output to stabilize.
Sensor Linearity
Linearity assesses how properly a sensor’s output corresponds to the enter pace. A linear sensor supplies a direct relationship between enter and output, whereas non-linear sensors exhibit deviations from this relationship. Assessing linearity entails measuring the sensor’s output at numerous speeds and plotting the outcomes. Deviations from a straight line point out non-linearity.
Sensor Noise Traits
Noise in a pace sensor represents undesirable fluctuations within the output sign. Noise can considerably have an effect on the accuracy and reliability of measurements. Varied methods can be utilized to guage noise traits. Generally used strategies embrace sign processing methods equivalent to spectral evaluation. This entails inspecting the frequency content material of the sensor’s output sign.
The magnitude of noise is usually expressed as a signal-to-noise ratio (SNR). Greater SNR signifies decrease noise ranges.
Sensor Decision
Decision refers back to the smallest detectable change in pace that the sensor can measure. Excessive decision is essential for functions requiring exact pace measurements. Decision is usually expressed as a proportion of the full-scale vary of the sensor. Measurement of decision entails figuring out the smallest discernible change in pace.
Testing Parameters Desk
The desk under Artikels the important thing testing parameters, their measurement items, and acceptable ranges for numerous pace sensor varieties. This desk supplies a fast reference for evaluating pace sensor efficiency.
Parameter | Measurement Unit | Acceptable Vary (Instance) | Sensor Kind |
---|---|---|---|
Accuracy | % Error | ±1% | Optical |
Precision | Customary Deviation | ≤0.5% | Magnetic |
Response Time | ms | ≤10ms | Ultrasonic |
Linearity | % Error | ±0.5% | Rotary |
Noise | dB | ≥ 60 dB | Corridor Impact |
Decision | RPM | 1 RPM | All Varieties |
Troubleshooting Methods
Troubleshooting pace sensors requires a scientific method to pinpoint the supply of the issue. Incorrect sensor readings can result in inaccurate pace calculations, impacting car efficiency, security techniques, and total performance. This part particulars widespread faults, diagnostic strategies, and corrective actions.
Widespread Velocity Sensor Faults and Their Causes
Velocity sensors, essential for correct pace measurement, can malfunction because of numerous elements. These points usually manifest as erratic pace readings, fluctuating alerts, or full lack of pace information. Understanding the potential causes of those issues is important for efficient prognosis.
- Wiring Points: Issues with the wiring harness, together with breaks, shorts, or free connections, can result in intermittent or full sign loss. Incorrect wiring or improper grounding may contribute to misguided pace information.
- Sensor Harm: Bodily harm to the sensor, equivalent to affect, corrosion, or contamination, can disrupt its capacity to precisely detect the rotational pace. The sensor’s inner elements may be broken, affecting its output.
- Sign Interference: Exterior electromagnetic interference (EMI) from different electrical elements within the car can disrupt the pace sensor’s sign. This could trigger inaccurate or fluctuating pace readings. Close by radio transmitters, poorly shielded wires, or defective electrical techniques are examples of potential sources.
- Mechanical Points: Mechanical issues with the linked shaft, equivalent to put on and tear, misalignment, or binding, can affect the sensor’s capacity to precisely measure rotation. A misaligned shaft, for example, will trigger the sensor to obtain an inconsistent sign, leading to incorrect pace readings.
- Energy Provide Issues: An inadequate or unstable energy provide can compromise the pace sensor’s operation, resulting in unreliable readings or sign dropout. A defective energy provide could cause the sensor to malfunction and even fail.
Diagnostic Steps for Velocity Sensor Points
A scientific method is essential for figuring out the basis reason for pace sensor issues. This entails a mixture of visible inspections, electrical checks, and information evaluation.
- Visible Inspection: Fastidiously examine the wiring harness for any seen harm, equivalent to cuts, fraying, or corrosion. Verify the sensor itself for bodily harm or contamination. Study the connection factors for correct connections and indicators of looseness.
- Electrical Checks: Use a multimeter to confirm the voltage and present ranges on the sensor’s energy and sign strains. Make sure that the voltage ranges are throughout the specified vary for the sensor’s operation. Evaluate these values to the producer’s specs.
- Sign Evaluation: Monitor the pace sensor’s output sign utilizing an oscilloscope or an acceptable diagnostic instrument. Observe the sign waveform for any irregularities, equivalent to lacking pulses, noise, or erratic fluctuations. Determine any anomalies within the sign sample that might point out the supply of the issue.
- Mechanical Checks: If relevant, examine the mechanical elements linked to the sensor for any indicators of damage, misalignment, or binding. Make sure the shaft or gear is correctly aligned with the sensor.
Corrective Actions for Velocity Sensor Malfunctions
As soon as the supply of the pace sensor malfunction is recognized, acceptable corrective actions could be carried out. These options vary from easy repairs to extra in depth replacements.
- Wiring Repairs: Restore or substitute broken wiring, making certain correct connections and grounding. Use high-quality wiring and connectors to forestall future points.
- Sensor Alternative: If the sensor is broken past restore, substitute it with a brand new, suitable unit. Comply with the producer’s directions for correct set up.
- EMI Shielding: Implement shielding measures to cut back electromagnetic interference. Use shielded cables and acceptable grounding methods.
- Mechanical Changes: Handle any mechanical points, equivalent to misalignment or put on, by realigning the shaft or changing worn elements.
- Energy Provide Verify: Guarantee the facility provide to the sensor is secure and throughout the specified vary. Verify for another linked gadgets that may be drawing an excessive amount of energy, affecting the sensor.
Troubleshooting Desk
Velocity Sensor Challenge | Potential Causes | Diagnostic Steps | Corrective Actions |
---|---|---|---|
Erratic Velocity Readings | Wiring points, sign interference, sensor harm, mechanical issues | Visible inspection, electrical checks, sign evaluation, mechanical checks | Restore/substitute wiring, add EMI shielding, substitute sensor, realign mechanical elements |
Lack of Velocity Sign | Wiring breaks, sensor harm, energy provide issues | Visible inspection, electrical checks, sign evaluation, energy provide checks | Restore/substitute wiring, substitute sensor, verify energy provide |
Fluctuating Velocity Sign | Sign interference, free connections, mechanical points | Sign evaluation, visible inspection, mechanical checks | Enhance shielding, tighten connections, realign mechanical elements |
Case Research
Analyzing pace sensor efficiency in numerous functions is essential for choosing the optimum sensor and making certain correct measurements. Completely different environments and functions impose distinctive challenges on pace sensors, requiring cautious consideration of things equivalent to working temperature, vibration, and electromagnetic interference. These case research spotlight the sensible software of pace sensor testing methodologies and supply invaluable insights into sensor efficiency in real-world situations.Understanding the efficiency traits of various pace sensor varieties in particular functions permits for knowledgeable choices and enhances system reliability.
These case research present sensible examples, enabling readers to guage and examine numerous sensor applied sciences for his or her particular wants.
Automotive Velocity Sensor Testing
Automotive functions demand excessive accuracy and reliability in pace measurements. These sensors are sometimes subjected to harsh environments, together with vibrations and temperature fluctuations. Correct choice and testing are essential for making certain constant efficiency below demanding situations.
“In a current examine on automotive pace sensors, a Corridor-effect sensor exhibited larger accuracy than an inductive sensor in a variety of testing environments. The Corridor-effect sensor maintained constant efficiency even below excessive vibration situations, whereas the inductive sensor confirmed fluctuations in readings.”
Sensor Kind | Atmosphere | Outcomes | Evaluation |
---|---|---|---|
Corridor-effect | Excessive vibration check rig | Minimal fluctuation in readings | Wonderful stability, appropriate for demanding automotive functions. |
Inductive | Excessive vibration check rig | Fluctuation in readings noticed | Prone to vibration; would possibly require further isolation measures. |
Industrial Equipment Velocity Sensor Testing
Industrial equipment usually requires exact pace monitoring for management and upkeep functions. The selection of pace sensor immediately impacts the accuracy and reliability of your complete system. The surroundings can range significantly from managed manufacturing unit flooring to out of doors gear.
“A examine on industrial equipment pace sensors in contrast the efficiency of optical and ultrasonic sensors in a high-dust surroundings. The optical sensor confirmed a big drop in accuracy because of mud accumulation, whereas the ultrasonic sensor maintained constant readings regardless of the difficult situations.”
- Optical Sensors: Prone to mud and particles accumulation, resulting in inaccurate readings in harsh environments.
- Ultrasonic Sensors: Sturdy and fewer affected by environmental elements like mud, making them an acceptable selection for industrial settings with potential contamination.
Robotics Velocity Sensor Testing
In robotics functions, pace sensors are essential for exact management and motion. The accuracy and responsiveness of the sensors immediately affect the efficiency of the robotic. Components just like the working vary and sensitivity to exterior interference have to be thought of.
“A comparative examine of various magnetic encoders for robotic functions confirmed that the incremental encoder exhibited superior efficiency when it comes to decision and response time. Absolutely the encoder, whereas offering absolute place information, confirmed slower response occasions.”
Security Precautions
Velocity sensor testing and upkeep require meticulous consideration to security protocols. Ignoring these precautions can result in severe damage or gear harm. Understanding the potential hazards and implementing acceptable security measures is paramount.
Normal Security Procedures
Correct private protecting gear (PPE) is essential for all testing procedures. This contains, however isn’t restricted to, security glasses, gloves, and acceptable footwear. Work areas needs to be stored clear and arranged to reduce the chance of tripping or falls. All personnel concerned within the testing course of needs to be adequately skilled in security procedures and emergency protocols.
Potential Hazards
Velocity sensors can function at excessive voltages, doubtlessly inflicting electrical shock. Mechanical elements can malfunction, resulting in transferring elements and sharp edges, posing a danger of cuts or lacerations. Incorrect dealing with of sensors or related wiring can result in brief circuits or fires. The surroundings the place pace sensors are examined might comprise hazardous supplies or chemical substances, requiring particular dealing with precautions.
Excessive-Voltage Security
When working with pace sensors that function at excessive voltage, isolating the facility supply is important. By no means try and work on a reside circuit. Use acceptable voltage-measuring gear and security procedures to find out the voltage degree earlier than beginning any work. Educated personnel needs to be accountable for high-voltage operations.
Hazardous Materials Dealing with
If the testing entails hazardous supplies, comply with established procedures for dealing with and disposal. Seek the advice of Materials Security Knowledge Sheets (MSDS) for particular precautions and security protocols. Use acceptable containment and protecting gear to forestall spills and publicity. Acceptable air flow could also be essential to keep away from inhalation hazards.
Security Precautions Throughout Testing Steps
- Powering On/Off: All the time guarantee the facility supply is remoted earlier than beginning any work on the pace sensor. Seek the advice of the producer’s directions for correct shutdown procedures. Potential hazards: electrical shock, hearth. Protecting measures: use lockout/tagout procedures, use voltage detectors, put on insulated gloves and security glasses.
- Wiring Connections: Fastidiously examine wiring connections for any harm or free connections. Guarantee correct grounding to forestall brief circuits. Potential hazards: electrical shock, hearth. Protecting measures: use insulated instruments, guarantee correct grounding, have a professional electrician for complicated wiring points.
- Calibration and Adjustment: When calibrating or adjusting the pace sensor, deal with elements with care to forestall harm. Guarantee correct torque values when tightening screws or fasteners. Potential hazards: mechanical damage, harm to elements. Protecting measures: use acceptable instruments, put on security glasses, comply with producer’s specs for calibration.
- Sensor Elimination and Set up: Use correct lifting gear for heavy sensors or elements. Guarantee correct alignment throughout set up. Potential hazards: mechanical damage, harm to elements, improper alignment. Protecting measures: use lifting gadgets, put on security glasses, verify sensor compatibility with the machine.
- Testing in Hazardous Environments: If the testing is carried out in a hazardous surroundings, guarantee correct security protocols are adopted, together with use of respirators and private protecting gear acceptable for the particular surroundings. Potential hazards: publicity to hazardous supplies, fumes, gases. Protecting measures: use acceptable PPE, comply with MSDS tips, seek the advice of security information sheets for the surroundings.
Emergency Procedures
Develop and talk a complete emergency response plan for the pace sensor testing surroundings. Set up clear procedures for dealing with accidents or incidents. This plan ought to embrace procedures for reporting accidents, calling emergency providers, and initiating first assist. Guarantee all personnel are conscious of the situation of emergency gear, equivalent to hearth extinguishers and first-aid kits.
Final Recap
So, you’ve got discovered methods to check pace sensors, from figuring out potential issues to performing correct calibrations. Keep in mind, meticulous testing results in dependable efficiency and long-lasting effectivity. This information supplies a complete overview, however observe makes good. Maintain experimenting and refining your testing method for one of the best outcomes. Prepared to overcome your pace sensor challenges?
Detailed FAQs
What are the widespread kinds of pace sensors?
Optical, magnetic, ultrasonic, and inductive sensors are widespread varieties. Every works on completely different ideas and has its personal strengths and weaknesses.
What gear do I want to check a pace sensor?
Relying on the sensor kind, you would possibly want a multimeter, oscilloscope, sign generator, and maybe specialised calibration gear. The precise instruments shall be decided by the kind of sensor and your testing strategies.
How do I interpret the outcomes of a pace sensor check?
Analyze the output alerts, noting any discrepancies from anticipated readings. Evaluate your outcomes to established requirements and specs on your explicit sensor kind. A desk exhibiting anticipated ranges for every parameter could be actually useful.
What are some widespread pace sensor faults?
Wiring points, broken elements, or environmental elements could cause issues. Take note of uncommon noises, erratic readings, or full sensor failure.