How lengthy does it take to construct a deck? This is not nearly lumber and nails; it is an entire undertaking, from preliminary blueprints to the ultimate, satisfying reveal. Elements like deck measurement, design intricacy, and the supplies chosen all play a vital position within the total timeline. Let’s break down the important thing components that have an effect on the development course of, from planning and design to the precise constructing part.
From a easy wood platform to a multi-level masterpiece full with a gazebo, the development time varies considerably. Understanding these variations will enable you to anticipate the timeframe and handle expectations. We’ll additionally discover frequent delays and methods for avoiding them, making certain your dream deck turns into a actuality with out pointless stress.
Mission Scope and Elements Affecting Time
Constructing a deck, from a easy wood platform to a posh multi-level construction, is a major enterprise requiring cautious planning and consideration of quite a few elements. The ultimate building time is closely influenced by the undertaking’s scope, supplies, and the presence of specialised options. Understanding these variables is essential for owners and contractors alike to precisely estimate undertaking completion dates and handle expectations.
Deck Dimension and Design Complexity
The scale and design complexity of a deck are basic determinants of the general building time. A small, easy deck constructed from available supplies will sometimes take significantly much less time to assemble than a big, multi-level deck with intricate options like stairs, railings, and built-in seating. Elaborate designs, incorporating options like gazebos, pergolas, or personalized lighting, will invariably enhance the development length.
Moreover, the intricacy of the design’s architectural components considerably influences the time wanted for fabrication and meeting.
Materials Choice and Availability, How lengthy does it take to construct a deck
The selection of supplies performs a vital position in figuring out the development timeframe. Utilizing available and readily processed supplies usually accelerates the method. For instance, pressure-treated lumber is a standard selection for its sturdiness and velocity of processing. Conversely, unique hardwoods or custom-designed supplies could necessitate extra time for procurement and specialised fabrication, lengthening the general building interval.
Moreover, the supply of the chosen supplies can affect the timeframe, with delays probably occurring if supplies must be ordered or shipped from distant places.
Particular Options and Their Affect
Incorporating particular options, resembling stairs, railings, built-in seating, or outside kitchens, will undoubtedly add to the general building time. The design and set up of those options require extra specialised labor, probably involving extra permits and inspections. As an example, establishing a posh staircase with intricate balustrades or a custom-designed outside kitchen will sometimes take longer than including a easy railing.
Deck Varieties and Development Timelines
Several types of decks have various building timelines. A easy wood platform, usually consisting of decking boards and helps, may be constructed comparatively shortly. Conversely, a multi-level deck with a gazebo or pergola, requiring extra advanced framing, roofing, and ending, will take significantly longer. Moreover, the incorporation of specialised components, like a built-in hearth or an built-in sound system, additional prolongs the undertaking’s completion.
Common Development Time for Totally different Deck Sizes
Deck Dimension | Supplies | Complexity | Estimated Time (Weeks) |
---|---|---|---|
Small (100 sq ft) | Stress-treated lumber, composite decking | Easy platform | 2-4 |
Medium (200 sq ft) | Stress-treated lumber, composite decking | Easy platform with stairs | 4-6 |
Giant (300+ sq ft) | Stress-treated lumber, composite decking, concrete | Multi-level, gazebo | 6-12+ |
Potential Delays and Mitigation Methods
Reason behind Delay | Impact | Mitigation Methods |
---|---|---|
Materials shortages | Mission standstill, prolonged timelines | Supply different supplies, safe early materials orders |
Adversarial climate situations | Delayed outside work, potential injury to supplies | Modify work schedule, use protecting coverings |
Unexpected structural points | Important price overruns, undertaking delays | Thorough website inspections, hiring certified inspectors |
Allowing issues | Mission delays, sudden hold-ups | Acquire crucial permits prematurely, have interaction with native authorities early |
Labor shortages | Slowed progress, missed deadlines | Have interaction a number of contractors, make the most of pre-fabrication |
Materials Choice and Affect on Timeline
Deciding on the correct supplies for a deck is essential, not only for aesthetics but in addition for the undertaking’s total timeline. The kind of wooden, composite, or railing materials considerably influences the time wanted for reducing, assembling, and set up. Selecting correctly can streamline the method and stop expensive delays.Wooden varieties, from pressure-treated lumber to unique hardwoods, play a major position in building length.
The inherent traits of every materials—like moisture content material, density, and grain patterns—have an effect on the reducing and shaping course of. Moreover, the complexity of the design, together with the variety of assist beams and the intricate particulars of the railing, instantly influences the time required.
Affect of Wooden Kind on Construct Time
Totally different wooden varieties exhibit various ranges of sturdiness and workability, impacting the general construct time. Stress-treated lumber, a well-liked selection for its resistance to rot and decay, usually requires much less ending and upkeep, which may translate to a faster set up. Cedar and redwood, recognized for his or her pure magnificence and resistance to bugs, sometimes require extra time for staining or sealing, lengthening the construct course of.
The drying time for the wooden additionally performs a vital issue, and in some circumstances, a delay could be wanted for correct drying.
- Stress-treated lumber, resulting from its pre-treatment, usually leads to sooner set up occasions in comparison with different wooden varieties. It’s because the pre-treatment minimizes the necessity for on-site remedies, saving helpful time.
- Cedar and redwood, owing to their pure magnificence and inherent properties, usually require extra time for staining or sealing. These processes want cautious consideration, probably resulting in delays within the undertaking timeline.
- Unique hardwoods, with their distinctive traits, could necessitate specialised instruments and methods, probably resulting in elevated building time.
Affect of Composite Decking Supplies on Timeline
Composite decking supplies, engineered from plastic and wooden fibers, are gaining reputation for his or her low upkeep and lengthy lifespan. The manufacturing course of for composite decking is commonly extra streamlined in comparison with conventional wooden, permitting for sooner meeting on-site. Nonetheless, the precise design and complexity of the deck’s options will nonetheless have an effect on the timeline.
- Composite decking usually is available in pre-fabricated panels, decreasing the quantity of on-site reducing and shaping required, resulting in a probably shorter building timeline.
- The necessity for specialised instruments or tools for putting in composite decking can be an element within the total undertaking time.
- Composite decks would possibly require exact measurements and becoming, probably resulting in minor delays.
Affect of Railing Materials on Set up Time
The selection of railing materials considerably impacts the set up time. Wooden railings, whereas visually interesting, usually require extra time for ending and set up. Steel railings, then again, may be sooner to put in however could require specialised instruments and experience. Glass railings, usually used for contemporary designs, may be extra advanced to put in and should contain extra security measures, probably resulting in delays.
- Wooden railings, resulting from their design, may be labor-intensive and require extra time for ending and set up in comparison with metallic or glass.
- Steel railings, with their standardized elements, usually provide a faster set up time in comparison with wooden, given correct experience.
- Glass railings, whereas visually interesting, could require specialised set up methods and security issues, rising the general set up time.
Planning and Design Concerns
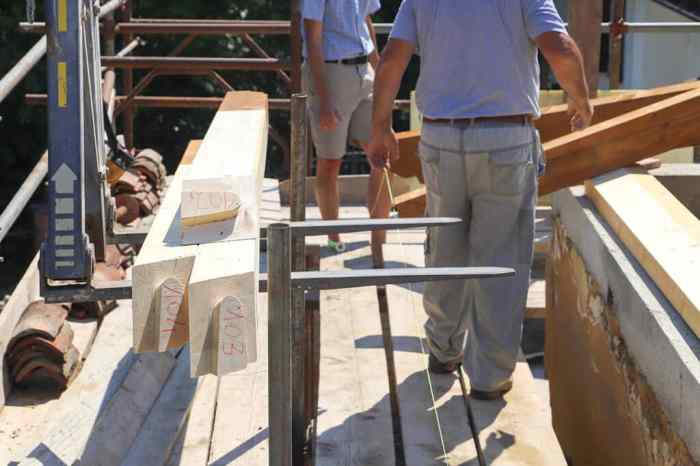
Cautious planning is essential for a profitable and well timed deck building undertaking. Thorough pre-construction steps decrease potential delays and make sure the ultimate product meets the home-owner’s imaginative and prescient. Understanding the intricate interaction between design, website preparation, allowing, and subcontractor coordination instantly impacts the undertaking’s total length.
Important Planning Steps
A well-defined plan is the bedrock of any profitable deck building. Key planning steps considerably affect the undertaking timeline. These steps embrace detailed website surveys, correct measurements, and a complete design that accounts for native constructing codes and laws. An in depth plan permits for higher useful resource allocation, environment friendly materials procurement, and a extra exact timeline for every part of the undertaking.
- Detailed Web site Surveys and Measurements: Correct website surveys and measurements are important for correct design and building. An expert surveyor or contractor can determine any challenges or obstacles on the property, resembling uneven terrain, utilities, or current buildings. Exact measurements make sure the deck’s dimensions conform to the home-owner’s specs and native constructing codes. A website survey additionally aids in correct price estimation, because the true extent of labor turns into clear, minimizing future surprises.
- Complete Design and Drawings: An in depth design plan, together with blueprints and specs, ensures all components of the deck are exactly deliberate. This plan should deal with features like structural assist, railing design, materials selections, and connections to the home. Clear and complete drawings facilitate communication between the home-owner, the contractor, and any subcontractors concerned, decreasing misunderstandings and potential delays. Nicely-defined plans result in fewer on-site changes, contributing to a smoother building course of.
- Constructing Code Compliance: Understanding and adhering to native constructing codes is paramount. Constructing codes dictate security requirements, structural necessities, and accessibility pointers for decks. Consulting with native authorities and incorporating code necessities within the design part will forestall expensive and time-consuming revisions later within the course of. Failure to conform may end up in delays and even undertaking rejection, incurring additional prices and time.
Web site Preparation and Measurements Affect
Correct website preparation and correct measurements are foundational to a well timed building course of. These components instantly affect the development timeline by decreasing the chance of sudden points and delays.
- Affect of Uneven Terrain: Uneven terrain requires extra intensive website preparation, together with grading, leveling, and probably reinforcing the inspiration. If these points should not recognized and addressed throughout the preliminary survey, they’ll considerably extend the development course of. Correct website preparation, with exact grading and leveling, ensures the deck is secure and constructed to final.
- Correct Measurements: Inaccurate measurements can result in materials waste, expensive changes, and delays in building. An expert surveyor or contractor can assure correct dimensions, decreasing the probability of errors that have an effect on the timeline and the general funds. Measurements should align with the structural calculations to keep away from any unexpected issues.
Affect of Permits and Inspections
Acquiring crucial permits and present process inspections are integral components of the development course of. Delays in these processes can have a cascading impact on all the undertaking timeline.
- Allowing Course of Time: The time taken to acquire constructing permits varies relying on native laws and the complexity of the undertaking. The home-owner can streamline this course of by offering full and correct data to the related authorities, together with crucial documentation. Anticipating potential delays and having different plans for potential roadblocks is vital.
- Inspection Necessities: Inspections guarantee the development complies with native constructing codes and security requirements. The frequency and length of inspections are decided by native laws. Understanding these necessities and coordinating with the inspector will help decrease disruptions to the development schedule.
Affect of Subcontractors
Hiring subcontractors can streamline the undertaking however requires cautious planning and coordination. Their affect on the general timeline is critical, notably regarding allowing and scheduling.
- Subcontractor Coordination: Correct coordination with subcontractors is crucial for a easy workflow. Clear communication concerning timelines, tasks, and deadlines helps keep away from conflicts and delays. A well-defined undertaking schedule and clear communication channels with all subcontractors guarantee everybody works collectively towards a shared objective.
- Allowing and Scheduling Coordination: Subcontractors concerned within the undertaking could have their very own allowing necessities. Coordinating these necessities with the primary contractor’s schedule can have an effect on the general undertaking timeline. To reduce potential delays, all subcontractors ought to be made conscious of the general schedule, allowing necessities, and undertaking deadlines.
Development Strategies and Methods
Deciding on the suitable deck-building method is essential for a profitable undertaking, instantly impacting the general timeline and funds. Elements such because the chosen supplies, website situations, and the specified aesthetic play important roles in deciding on the optimum methodology. Totally different approaches provide various levels of complexity and velocity, which have to be fastidiously thought-about to make sure a undertaking stays on observe.
Comparability of Deck-Constructing Methods
Varied methods affect the development timeline and ultimate price. Publish-and-beam building, usually favored for its strong design, entails supporting the deck with vertical posts and horizontal beams. Ledger board strategies, sometimes employed for attaching decks to current buildings, are easier however could require extra website preparation. These strategies, together with different methods, require cautious planning and materials choice to fulfill the precise wants of every undertaking.
Affect of Prefabricated Elements
Prefabricated deck elements, resembling pre-cut lumber and pre-assembled railings, are gaining reputation. Their use considerably reduces on-site labor and potential delays, usually resulting in a shorter building timeline. Prefabricated components normally contain exact measurements and pre-assembly, minimizing errors and wasted time. Nonetheless, the price of these prefabricated elements have to be weighed in opposition to the potential for sooner building.
Timeline for Totally different Framing Strategies
The development timeline varies based mostly on the framing methodology employed. A post-and-beam deck, resulting from its extra advanced framework, usually takes longer to assemble than a ledger board deck. Estimating the precise time for every methodology relies on elements resembling the dimensions of the deck, the complexity of the design, and the supply of supplies and labor.
As an example, a 10×12 post-and-beam deck would possibly take 5-7 days for framing alone, whereas a comparable ledger board deck could possibly be accomplished in 3-5 days.
Typical Deck Development Course of
The deck building course of follows a collection of steps, every with an approximate length. These steps may be broadly categorized as follows:
- Web site Preparation (1-3 days): This entails clearing the world, leveling the bottom, and putting in crucial utilities. The precise length relies on the dimensions and situation of the location, probably requiring extra time for website remediation or excavation.
- Framing (2-7 days): That is the essential part the place the deck’s construction is constructed. The time required relies on the chosen framing methodology, the dimensions of the deck, and the complexity of the design. For instance, a bigger deck with intricate assist techniques will take longer to border.
- Decking Set up (1-5 days): This entails laying the decking boards. The length relies on the kind of decking materials, the dimensions of the deck, and the talent of the installers.
- Railing Set up (1-3 days): This step entails putting in railings, sometimes after the decking is full. The complexity of the railing design will affect the length.
- Ending (1-2 days): This consists of duties like sealing the deck and including any ending touches. The time wanted will rely upon the precise ending duties.
Labor and Staffing Concerns: How Lengthy Does It Take To Construct A Deck
Deciding on the correct labor drive is vital for a deck building undertaking. The supply and talent degree of the workforce, together with the necessity for specialised contractors, instantly impacts the undertaking’s length and total price. Sudden delays, usually stemming from climate or scheduling conflicts amongst tradespeople, can considerably alter the unique timeline. Understanding these elements permits for proactive planning and mitigation methods.
Affect of Labor Availability and Talent Degree
The supply of expert labor in a given space can considerably affect the undertaking timeline. Areas with a excessive demand for building employees would possibly face shortages, resulting in delays because the contractor struggles to seek out appropriate candidates. The talent degree of the crew additionally performs a vital position. A workforce with intensive expertise in deck building will probably full duties extra effectively, minimizing potential errors and accelerating the undertaking’s progress.
Conversely, a much less skilled crew could require extra supervision, rising the general undertaking length. In some circumstances, this would possibly even necessitate extra coaching or an extended interval for high quality management.
Affect of Specialised Contractors
Hiring specialised contractors, resembling carpenters, electricians, or plumbers, can considerably affect the undertaking length. Every commerce has distinctive necessities, together with particular licensing, permits, and specialised tools. Scheduling these contractors to work harmoniously and keep away from conflicts is essential. A talented undertaking supervisor can streamline the method, making certain environment friendly coordination between completely different trades. Delays can come up if specialised contractors are unavailable or if scheduling conflicts come up, which may affect all the undertaking’s timeline.
As an example, a delay in acquiring crucial electrical permits can delay all the set up course of.
Climate-Associated Delays
Climate situations can create substantial delays in deck building. Rain, robust winds, or excessive temperatures can halt work, probably delaying the undertaking for days and even weeks. Correctly contemplating climate patterns within the area and the undertaking timeline is vital. Development schedules ought to incorporate buffer time to account for unexpected climate occasions. The undertaking’s design and supplies should even be weather-resistant.
As an example, a undertaking scheduled for the wet season could require indoor work to guard the deck supplies.
Coordination of A number of Trades
Coordinating a number of trades, resembling plumbers, electricians, and landscapers, is crucial for a easy undertaking. Every commerce has particular timelines and duties that have to be executed in a coordinated method. Scheduling conflicts between completely different trades can result in delays. An efficient undertaking supervisor can mitigate these dangers by meticulous scheduling, clearly outlined tasks, and fixed communication between trades.
As an example, a delay within the plumbing work can disrupt the electrician’s schedule, resulting in cascading results all through the undertaking. To keep away from such eventualities, an in depth schedule with overlapping duties, together with buffer time, is crucial.
Actual-World Examples
Deck building initiatives fluctuate extensively in scope, from easy additions to elaborate designs. Understanding the real-world utility of those elements is essential for correct estimations and profitable undertaking completion. This part delves into particular examples, highlighting profitable and less-successful initiatives, to offer a sensible understanding of all the course of.
Case Research of Deck Tasks
Actual-world deck initiatives provide helpful insights into the complexities of building. The scope, supplies, and timelines can fluctuate dramatically, influenced by design selections, website situations, and contractor experience. Inspecting these initiatives offers a sensible perspective on the elements that affect undertaking outcomes.
- Mission A: A home-owner commissioned a 12×16-foot wood deck addition. The undertaking utilized pressure-treated lumber for the framing and composite decking for the floor. The undertaking spanned 10 weeks, together with allow acquisition, materials supply, and building. This undertaking demonstrated a comparatively easy construct with a predictable timeline, because of the clear scope and uncomplicated design.
- Mission B: A home-owner sought a posh, multi-level deck with intricate railing designs and a pergola. The undertaking used composite decking, metal framing, and unique hardwoods for the railings. The undertaking timeline stretched to 16 weeks because of the intricate design, specialised supplies, and the necessity for exact craftsmanship.
- Mission C: This undertaking concerned a deck renovation incorporating a scorching tub. The scope included eradicating an current deck, putting in new helps, and working electrical for the recent tub. The unique estimate was 8 weeks, however unexpected points with the present basis prolonged the undertaking to 12 weeks. This illustrates how sudden website situations can considerably affect the timeline.
Delayed Deck Mission Case Examine: Mission D
Mission D, a 15×20-foot deck with a {custom} railing system, confronted delays resulting from a number of elements. The preliminary estimate was 12 weeks, nevertheless it prolonged to 18 weeks.
- Unexpected Soil Situations: Subsurface points have been found throughout excavation, requiring extra reinforcement and redesign, delaying the undertaking by 4 weeks.
- Materials Shortages: Sudden delays within the supply of {custom} railing supplies prolonged the timeline by 2 weeks.
- Contractor Scheduling Conflicts: The contractor skilled conflicts with different initiatives, impacting the supply of expert labor and pushing the completion date again by 2 weeks.
The undertaking taught helpful classes, together with the significance of thorough website assessments, contingency planning for materials delays, and the need of clear communication between the home-owner and contractor.
Estimating Deck Development Prices
Correct price estimation is crucial for budgeting and managing undertaking expectations. The next desk Artikels the elements impacting price and offers an instance of an estimated price for a 10×12-foot deck utilizing pressure-treated lumber and composite decking.
Issue | Description | Estimated Price (USD) |
---|---|---|
Supplies | Stress-treated lumber, composite decking, fasteners, and {hardware} | $3,500 |
Labor | Carpenter labor, together with framing, decking, and railing set up | $4,000 |
Allowing | Acquiring crucial permits and inspections | $200 |
Contingency | Buffer for sudden prices or delays | $500 |
Whole Estimated Price | $8,200 |
Observe: Prices are estimates and may fluctuate based mostly on location, materials high quality, and labor charges.
Deck Development Timeline
A visible illustration of a typical deck building timeline helps illustrate the varied levels and anticipated durations.
[A visual representation of a timeline would be displayed here. This would include phases like site preparation, framing, decking, railing installation, and final inspection. Each phase would be labeled and have an estimated duration.]
Ending Remarks
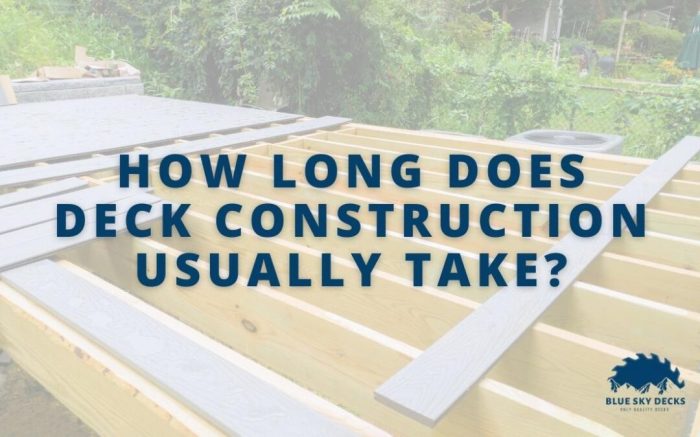
Constructing a deck is a rewarding undertaking, however figuring out the anticipated timeline is essential. This information has illuminated the important thing elements influencing building length, from materials choice to labor issues. By understanding these variables, you possibly can higher estimate the time required and proactively deal with potential delays. Bear in mind, a well-planned undertaking is a undertaking accomplished on time and inside funds.
Now, go forth and construct your dream deck!
Query Financial institution
How a lot does a deck price, on common?
Common deck prices fluctuate extensively relying on measurement, supplies, and complexity. Count on to see costs starting from a number of thousand to tens of hundreds of {dollars}. Detailed quotes from contractors are important for correct price estimates.
What permits are wanted for deck building?
Allow necessities fluctuate by location. At all times test along with your native constructing division for particular laws concerning deck building, together with measurement limitations and crucial inspections.
What are some frequent causes of delays in deck initiatives?
Delays can stem from unexpected climate situations, materials shortages, allow points, or difficulties coordinating a number of trades. Cautious planning and contingency measures can decrease these dangers.
How do I select the correct supplies for my deck?
Think about elements like funds, aesthetic preferences, and long-term upkeep wants when deciding on supplies. Stress-treated lumber is a well-liked selection for its sturdiness, whereas composite decking provides low-maintenance enchantment. Wooden varieties like cedar and redwood even have their very own professionals and cons.