flush a outdated forged iron fuel boiler system is an important process for sustaining its effectivity and longevity. These growing older methods, usually that includes intricate forged iron elements, can accumulate sediment and mineral deposits over time, hindering optimum efficiency. This information offers a complete overview of the method, protecting security precautions, preparation steps, flushing procedures, and post-flush checks, making certain a secure and efficient cleanout.
Understanding the particular traits of your forged iron fuel boiler system is significant for a profitable flush. The intricate design and potential for blockages require a meticulous method. This information will stroll you thru the mandatory steps to realize a clear and environment friendly system, whereas highlighting the significance of security measures all through the method.
Introduction to Previous Solid Iron Gasoline Boiler Methods
Forged iron fuel boilers, as soon as ubiquitous in properties and companies, symbolize a captivating chapter within the historical past of heating expertise. Their sturdy development and effectivity, although usually much less subtle than trendy designs, made them a reliable answer for heat for a lot of many years. Understanding these methods, their strengths, and weaknesses, is essential for anybody contemplating their restore or alternative.These boilers, usually constructed from heavy forged iron, are characterised by an enormous warmth exchanger, usually that includes intricate inside fins and chambers for optimum warmth switch.
The design, whereas easy in its elementary components, usually integrated intricate patterns and designs, reflecting the craftsmanship of the period. Their massive dimension and substantial weight contribute to their attribute thermal mass, permitting them to retailer and launch warmth successfully, a key issue of their effectivity.Widespread issues related to older forged iron fuel boilers usually stem from their age and the supplies used of their development.
Corrosion, particularly from the interplay of water and the metallic, can result in leaks and diminished effectivity. Sediment buildup within the system can limit water stream and impede warmth switch. Moreover, the intricate nature of the inner elements could make upkeep and restore extra advanced. A radical understanding of those potential points can stop pricey repairs and preserve the boiler’s efficiency.
Typical Elements of an Previous Solid Iron Gasoline Boiler System
Understanding the elements of an outdated forged iron fuel boiler system is important for prognosis and restore. This desk particulars the standard elements, their perform, and potential points, alongside troubleshooting steps.
Part | Description | Potential Challenge | Troubleshooting |
---|---|---|---|
Burner Meeting | The burner ignites the gas and mixes it with air for combustion. | Burner not igniting, uneven flame, sputtering sounds. | Verify fuel provide, burner nozzles, and igniter. Clear burner elements. |
Warmth Exchanger | The core part the place warmth is transferred from the combustion gases to the water. | Corrosion, leaks, sediment buildup. | Examine for leaks, scale, or corrosion. Contemplate a chemical flush to take away sediment. |
Enlargement Tank | Maintains stress within the system. | Low stress, stress fluctuations. | Examine the tank for leaks and guarantee it’s appropriately sized for the system. |
Water Circulation Pump | Strikes the water all through the system. | Pump not working, noisy pump. | Verify for blockages, examine pump for injury or worn elements. |
Management Valve | Regulates the stream of fuel and water to the system. | Improper fuel stress, inconsistent water temperature. | Alter settings in line with producer specs. Verify for leaks and obstructions. |
Flue System | Permits exhaust gases to exit the system safely. | Blocked flue, inadequate venting. | Clear the flue recurrently. Guarantee correct air flow is maintained. |
Move of Water By way of the System
The diagram beneath illustrates the fundamental stream of water by means of a typical forged iron fuel boiler system. Water enters the boiler and flows by means of the warmth exchanger. The heated water then travels to the radiators or different heating components all through the constructing. After passing by means of the heating components, the water returns to the boiler, finishing the cycle.
(Think about a easy diagram right here. A closed loop with arrows indicating water stream from the boiler to radiators and again. Label the important thing elements like boiler, radiators, and enlargement tank.)
Understanding the Flushing Course of
A meticulously executed flush is paramount to the longevity and optimum efficiency of any forged iron fuel boiler system. This meticulous course of removes collected sediment and particles, making certain environment friendly warmth switch and stopping future points. Correct flushing not solely extends the boiler’s lifespan but in addition considerably reduces the chance of pricey repairs and replacements.The method of flushing an outdated forged iron fuel boiler system is essential for sustaining its effectivity and stopping future issues.
Sediment, scale, and corrosion merchandise construct up over time, hindering the boiler’s potential to switch warmth successfully. A radical flush removes these obstructions, restoring the system to peak efficiency and minimizing the chance of pricey repairs.
Function of Flushing
Flushing an outdated forged iron fuel boiler system is important to take away collected sediment, scale, and corrosion merchandise. These deposits limit water stream, decreasing warmth switch effectivity and doubtlessly resulting in overheating or injury to the boiler elements. Common flushing ensures optimum warmth output and extends the boiler’s lifespan.
Strategies for Flushing
Varied strategies exist for flushing a forged iron fuel boiler system. The most typical approaches are gravity and stress flushing. Gravity flushing depends on gravity to empty the system, whereas stress flushing makes use of a pump to pressure water by means of the system. The selection of technique usually is determined by the particular configuration of the system and the extent of blockage.
Gravity Flushing Process
Gravity flushing is an easy technique, supreme for methods with comparatively low stress.
- Isolate the System: Fully shut off the fuel provide to the boiler and isolate the water provide. It is a crucial security precaution to forestall any unintended water stream or fuel leaks.
- Drain the System: Open the drain valves on the lowest level of the system. Permit the water to empty utterly. This ensures the elimination of stagnant water which will comprise impurities.
- Flush with Contemporary Water: Fill the system with recent water, then open the drain valve once more. Repeat this course of a number of instances to flush out any sediment and particles. Make sure the water runs clear.
- Examine and Refill: Rigorously examine the drain valve for any important blockages. As soon as happy, refill the system with recent water and guarantee all valves are closed and safe.
- Confirm the System: Flip the fuel provide again on and test for any leaks or uncommon noises. Activate the boiler and monitor its operation.
Instruments and Supplies
The next instruments and supplies are usually wanted for a gravity flush:
- Adjustable wrench
- Drain valve keys
- Water hose
- Bucket
- Contemporary water provide
- Security glasses
- Gloves
Comparability of Flushing Strategies
Methodology | Benefits | Disadvantages |
---|---|---|
Gravity Flushing | Easy, comparatively cheap, much less advanced gear required. | Appropriate for smaller methods or methods with minimal blockage. Can take longer to clear important blockages. |
Stress Flushing | Extra environment friendly for eradicating important blockages, quicker. | Requires specialised gear (pump, filters), doubtlessly costlier. Requires extra experience to function safely. |
Security Precautions for Flushing
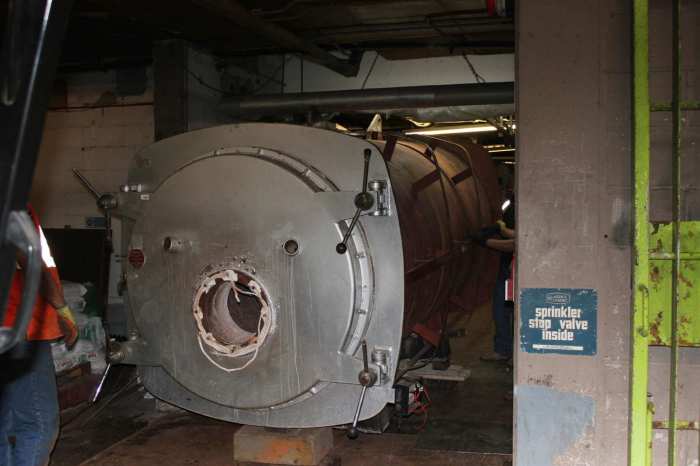
The fragile dance of sustaining a useful forged iron fuel boiler system necessitates meticulous consideration to security protocols. Neglecting these precautions can result in critical penalties, from minor accidents to catastrophic failures. Understanding the potential hazards inherent in working with fuel home equipment and water methods is paramount. Correct preparation and adherence to security tips will not be mere formalities; they’re the cornerstone of a profitable and safe flushing operation.Working with fuel boilers necessitates a profound understanding of potential hazards.
Leaks within the fuel strains, defective ignition methods, and improper venting can create flammable atmospheres. Contact with high-pressure water methods, significantly when mixed with the presence of mineral deposits, can result in slips, journeys, and falls. These dangers demand meticulous planning and execution.
Significance of Shutting Off Utilities
Making certain the security of the operation necessitates the entire shut-off of each the fuel provide and electrical energy to the boiler system. Failure to take action may end up in unintended ignition, electrical shocks, or different critical mishaps. This significant step eliminates the chance of uncontrolled fuel stream or electrical discharges through the flushing course of.
Pre-Flush Security Guidelines
A complete pre-flush security guidelines ensures all potential dangers are mitigated. Thorough preparation prevents sudden points and facilitates a easy, environment friendly flushing course of.
- Confirm the fuel provide is totally shut off on the primary fuel valve. This significant step eliminates the chance of unintended fuel leaks.
- Disconnect {the electrical} provide to the boiler. This prevents electrical shocks and associated risks through the flushing process.
- Examine all water connections for leaks. Leaks can create hazardous conditions and compromise the integrity of the system.
- Guarantee all stress reduction valves are functioning appropriately. This safeguards towards potential stress surges and subsequent system injury.
- Establish and isolate any potential hazards within the speedy neighborhood of the boiler system, corresponding to unstable buildings or uncovered wires. This proactive method mitigates potential accidents.
Dealing with Water and Chemical compounds
Protected dealing with of water and any related chemical compounds is essential through the flushing course of. Correct procedures decrease the chance of contamination and forestall accidents.
- Use acceptable private protecting gear (PPE), together with gloves and security glasses, to guard your self from potential splashes or contact with contaminants.
- Adhere to the producer’s directions when dealing with any chemical compounds used within the flushing course of. This ensures the right procedures are adopted.
- Correctly get rid of all chemical compounds and wastewater in line with native rules and environmental requirements. Accountable disposal prevents contamination of the encompassing atmosphere.
- Keep a clear and arranged workspace to forestall slips, journeys, and falls. A transparent work space is essential for security and effectivity.
Potential Hazards Related to Solid Iron Gasoline Boilers
Understanding the potential hazards related to forged iron fuel boilers is important for secure operation. These hazards embrace, however will not be restricted to, the potential for corrosion, leaks, and mineral deposits.
- Corrosion can result in leaks within the boiler system, posing a danger of fuel leaks and water injury. Proactive upkeep can mitigate this danger.
- Mineral deposits can scale back the effectivity of the boiler and improve the chance of blockage. Common flushing can stop this buildup.
- Gasoline leaks can create a flammable ambiance, posing a big hearth danger. Common inspections and upkeep are essential.
- Excessive-pressure water methods, if not dealt with correctly, can result in accidents from slips, journeys, and falls. Cautious dealing with and a focus to the encompassing atmosphere are important.
Preparation Earlier than Flushing
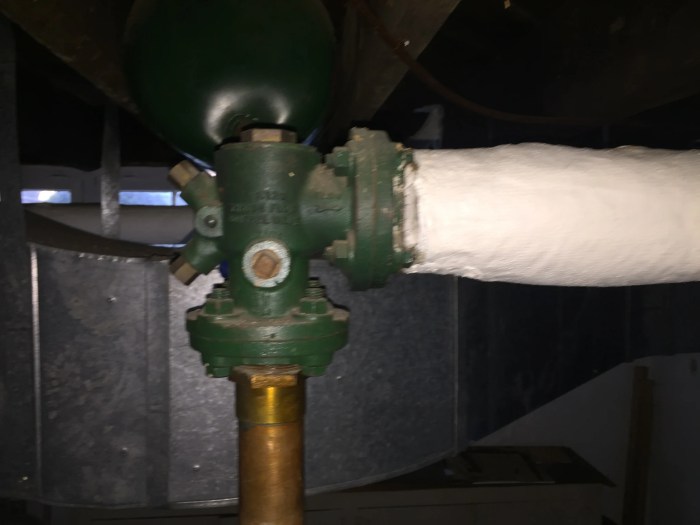
Unveiling the intricate dance of preparation is paramount earlier than embarking on the flushing ritual of your growing older forged iron fuel boiler. A radical pre-flushing routine ensures the method is environment friendly, secure, and in the end, efficient in revitalizing your heating system. Correct preparation minimizes potential hazards and maximizes the possibilities of a profitable flushing operation.A meticulously deliberate method to boiler system preparation includes complete steps.
This meticulous course of safeguards the integrity of the system and ensures the flushing process proceeds easily. The important thing lies in methodical execution and a deep understanding of the steps concerned.
Draining the System Fully
Thorough draining is important for a profitable flush. Incomplete drainage leaves residual water and particles within the system, doubtlessly hindering the effectiveness of the flushing course of and inflicting future issues. Making certain a whole drain prevents any remaining contaminants from being circulated all through the system through the flushing process. The aim is to get rid of all water from the system to keep away from potential water hammer and injury through the flushing course of.
Disconnecting the Boiler from the System
Exactly disconnecting the boiler from the remainder of the system is an important step. Improper disconnection can result in leaks, injury, or the potential for a hazardous state of affairs. Cautious elimination of connections and valves is important to forestall injury to the system. Disconnect the boiler from the provision and return pipes, and any related elements. This consists of isolating the boiler from the remainder of the heating circuit.
At all times seek the advice of the producer’s directions for the particular procedures associated to your boiler mannequin.
Eradicating Air and Trapped Water
Eradicating trapped air and water is crucial to the profitable operation of the flushing course of. Trapped air and water pockets can intrude with the stream of the flushing answer and forestall full cleansing of the system. Correct venting and air elimination earlier than commencing the flush process are paramount to keep away from obstructions. Utilizing acceptable instruments, corresponding to a valve or a bleed screw, to take away trapped air and water from numerous factors within the system is critical.
Guidelines for Making ready the Boiler for Flushing
This guidelines serves as a structured information to make sure a whole and environment friendly preparation of your forged iron boiler system for flushing.
Job | Description | Supplies | Process |
---|---|---|---|
Drain the system | Fully empty the boiler system of all water. | Drain valve key, container to catch the water | Open drain valves, accumulate drained water, and monitor till all water is gone. |
Disconnect the boiler | Isolate the boiler from the remainder of the heating circuit. | Applicable instruments (wrench, pliers), alternative elements if wanted. | Disconnect provide and return pipes, and any related elements. |
Take away trapped air and water | Eradicate air pockets and trapped water from the system. | Venting instruments (air bleed valves), appropriate rags | Find and open air vents, and launch any trapped water. |
Confirm System Empty | Affirm full elimination of water from the system. | Visible inspection | Verify for any remaining water within the boiler and pipes. |
Flushing Procedures
Unveiling the meticulous dance of water displacement, the flushing course of for an outdated forged iron fuel boiler system calls for a exact choreography of actions. This significant step ensures optimum efficiency, longevity, and the environment friendly elimination of collected sediment and particles, which may hinder the system’s warmth switch capabilities. The tactic chosen, often gravity-fed, dictates the sequence of occasions, however the underlying ideas of efficient water elimination and blockage identification stay fixed.The gravity-fed flushing technique, usually probably the most easy and cost-effective choice, leverages the pressure of gravity to effectively clear the system.
Correct method is paramount to make sure full and thorough elimination of impurities, stopping future points. Understanding the potential blockages and their options is equally important for a easy and profitable flushing operation.
Gravity Flushing Process
Gravity flushing capitalizes on the pure downward pull of water to take away trapped particles and sediment from the boiler system. This technique is comparatively easy to implement and requires minimal specialised gear. Exact execution is essential to making sure environment friendly water elimination.
Efficient Water Elimination Strategies
Maximizing water elimination includes a scientific method. Initially, open the drain valves on the lowest factors of the system, permitting the water to empty utterly. Then, slowly open the provision valve to fill the system with recent water. Repeating this course of, flushing the water and sediment out of the system in intervals, is essential. The method ought to proceed till the water runs clear.
Figuring out and Addressing Blockages
Throughout the flushing course of, pay shut consideration to the outflow. Uncommon delays or modifications within the stream charge can point out blockages. Understanding the potential sources of blockages and their options is significant. Blockages can vary from sediment build-up to overseas objects which have change into lodged throughout the system.
Forms of Blockages and Options
- Sediment Buildup: Sediment accumulation is a standard prevalence in older methods. The constant flushing course of helps to take away this buildup. In additional cussed instances, specialised cleansing brokers could be needed. In some situations, an intensive inspection by a certified technician could be wanted to deal with important sediment accumulation.
- International Objects: International objects, corresponding to small items of particles, can change into lodged within the system. These will be eliminated by fastidiously inspecting the system, usually involving the help of a certified skilled. Utilizing specialised instruments for cleansing and clearing out the blockage is commonly required.
- Air Pockets: Air pockets can impede the stream of water and create stress imbalances throughout the system. These are generally recognized by the presence of intermittent water stream or an lack of ability to totally fill the system. Cautious venting of the system to launch these pockets is a key side of the flushing course of.
Flushing Course of Desk
Step | Process | Potential Challenge | Decision |
---|---|---|---|
1 | Open drain valves on the lowest factors. | Valve is caught or defective. | Tighten the valve or change it if needed. |
2 | Slowly open the provision valve to fill the system. | Provide valve is defective. | Examine and restore the provision valve. |
3 | Repeat the filling and draining course of a number of instances. | Water stream is sluggish or intermittent. | Verify for blockages; examine the system for overseas objects. If needed, search skilled help. |
4 | Monitor the outflow for readability. | Water stays cloudy or discolored. | Proceed flushing till the water runs clear. If the issue persists, search skilled help. |
Submit-Flushing Procedures
The flushing course of, whereas essential for rejuvenating an growing older forged iron fuel boiler system, is just half the battle. Correct post-flush procedures are important for making certain the system’s longevity and environment friendly operation. A well-maintained system will provide years of dependable heating. These procedures make sure the system is restored to its optimum efficiency and security requirements, prepared for continued use.The meticulous execution of post-flush procedures ensures that the boiler system just isn’t solely clear but in addition absolutely operational and secure.
This includes cautious reconnection, leak testing, and a complete system test to make sure every part is functioning appropriately.
Thorough System Rinsing
Submit-flushing, a whole rinse is crucial to take away any residual flushing chemical compounds or particles which will have lingered within the system. This remaining rinse ensures a clear, contaminant-free atmosphere throughout the pipes and boiler, stopping potential future issues. A radical rinse ensures the system’s inside elements will not be compromised by residual contaminants. The process includes working clear water by means of the system for a specified period.
Reconnecting the Boiler
Cautious reconnection of the boiler to the system is essential to keep away from leaks and injury. Every connection level have to be inspected for correct alignment and tightness earlier than securing. A misaligned or unfastened connection can result in important points, together with leaks and potential injury to the system. Utilizing the right instruments and adhering to the producer’s directions are paramount for a secure and efficient reconnection.
Leak Testing and Performance Verify
Testing for leaks and making certain the boiler’s performance after reconnection is a crucial security step. Leak testing includes visually inspecting all connections for indicators of water leakage and making use of stress to determine potential weak factors. The system’s performance is assessed by checking the heating output, temperature regulation, and different important facets of the boiler’s operation. Addressing any recognized points instantly is essential for the security and effectivity of the system.
Submit-Flush Checks Guidelines
This guidelines offers a structured method to post-flush procedures.
Job | Description | Supplies | Process |
---|---|---|---|
Disconnect Boiler from System | Detach the boiler from the system’s plumbing. | Adjustable wrench, pipe wrenches, acceptable instruments | Rigorously disconnect all pipes from the boiler. |
Thorough Rinse | Flush the system with clear water. | Water provide, timer, water hoses | Open the water provide and run water by means of the system for the required period. |
Reconnect Boiler | Reconnect the boiler to the system. | Plumbing fittings, pipe sealant | Guarantee all connections are tight and safe. |
Leak Take a look at | Verify for leaks round connections. | Water stress gauge, leak detection answer (optionally available) | Apply stress to the system and examine all connections for leaks. |
System Performance Take a look at | Take a look at the boiler’s heating output. | Thermometer, heating output measurement gear | Begin the boiler and monitor its heating output and temperature regulation. |
Troubleshooting Widespread Points
Unexpected circumstances can generally come up through the flushing technique of an outdated forged iron fuel boiler system. Understanding potential points and their options is essential for a profitable and secure process. This part offers a complete information to troubleshooting widespread issues, making certain a easy and environment friendly flushing operation.A meticulous method to figuring out and rectifying issues throughout flushing is paramount.
Cautious statement and a scientific troubleshooting technique are key to sustaining the integrity of the system and stopping additional issues. This part will Artikel the potential issues, their causes, and the suitable corrective actions.
Potential Points Throughout Flushing
A number of points can happen through the flushing course of, from minor inconveniences to important system failures. Figuring out these points promptly and addressing them successfully is crucial for stopping additional injury and making certain a profitable flushing operation.
Leak Detection and Restore
Leaks are a frequent concern throughout flushing. A methodical method to leak detection is important. Visible inspection of all pipe connections, joints, and fittings is step one. Hear for uncommon feels like hissing or dripping. Pay explicit consideration to areas the place pipes connect with the boiler, enlargement tanks, and radiators.
Utilizing a leak detection answer, like a soapy water combination, will help pinpoint the precise location of the leak. If a leak is found, instantly shut off the water provide to the system. Restore the leak promptly, utilizing acceptable fittings and supplies to forestall additional injury. If the leak is in depth or past your capabilities, seek the advice of a certified plumber.
Clogged Pipes
Clogged pipes can hinder the flushing course of, doubtlessly resulting in stress points or a whole blockage. If the system experiences a sudden lower in stress, or if water stream turns into sluggish, clogged pipes often is the wrongdoer. Utilizing a specialised pipe cleansing device, like a drain snake, can dislodge the clog. If the blockage is extreme, knowledgeable plumber could also be essential to clear the pipes.
Stress Points
Stress fluctuations through the flushing course of can point out numerous issues. Sustaining acceptable stress ranges is significant for the correct operation of the system. If the stress drops considerably, a leak within the system could also be current. If the stress rises unexpectedly, an air pocket might have fashioned, or there could also be a blockage within the system. Seek the advice of a certified plumber if the stress points persist or worsen.
Different Potential Issues
Different points would possibly come up through the flushing course of, together with points with the valves, the pump, or the enlargement tank. If the system reveals uncommon conduct, like a defective pump or valves, seek the advice of knowledgeable plumber to diagnose and restore the issue.
Troubleshooting Desk
Challenge | Description | Trigger | Resolution |
---|---|---|---|
Leak | Water leakage from pipe connections, joints, or fittings. | Free connections, broken pipes, or worn-out fittings. | Tighten connections, change broken pipes, or restore worn-out fittings. |
Clogged Pipes | Decreased or blocked water stream in pipes. | Accumulation of particles, sediment, or mineral deposits. | Use specialised instruments to clear blockages, or seek the advice of a plumber. |
Stress Fluctuations | Important modifications in water stress throughout flushing. | Leaks, air pockets, or blockages within the system. | Establish and restore leaks, tackle air pockets, or clear blockages. |
Valve Malfunction | Defective operation of valves within the system. | Broken valves or worn-out elements. | Exchange defective valves or seek the advice of a plumber. |
Detailed Process for Figuring out and Fixing Leaks
- Visible Inspection: Rigorously examine all pipe connections, joints, and fittings for any indicators of leakage. Pay explicit consideration to areas with excessive stress or stress factors.
- Auditory Inspection: Hear for uncommon feels like hissing or dripping. These sounds can pinpoint the precise location of the leak.
- Soapy Water Take a look at: Apply a soapy water combination to suspected areas. Bubbles point out the presence of a leak.
- Shut-Off Valves: Instantly shut off the water provide to the system if a leak is discovered.
- Restore: Restore the leak utilizing acceptable fittings and supplies, making certain a safe and watertight seal. If the leak is in depth or past your capabilities, seek the advice of a certified plumber.
Upkeep and Preventative Measures
A well-maintained forged iron fuel boiler system ensures longevity, optimum efficiency, and security. Common preventative measures can considerably scale back the probability of pricey repairs and breakdowns, extending the lifetime of your funding. Proactive upkeep not solely saves cash but in addition protects the atmosphere by maximizing power effectivity.Forged iron boilers, attributable to their inherent design and the potential for mineral buildup and corrosion, require particular upkeep protocols.
Ignoring these protocols can result in decreased effectivity, elevated gas consumption, and even full system failure. Understanding the significance of normal inspections and preventative actions is essential for making certain a easy and dependable operation.
Significance of Common Upkeep
Common upkeep is paramount to the continued operational effectivity and lifespan of a forged iron fuel boiler system. Constant checks and preventative actions decrease the chance of sudden breakdowns, extending the system’s service life and decreasing the necessity for pricey repairs. Correct upkeep additionally helps preserve power effectivity, decreasing gas consumption and reducing working prices.
Preventative Measures to Keep away from Future Points
A number of preventative measures will help keep away from future points together with your forged iron fuel boiler. These measures embrace common water high quality checks, meticulous cleansing of the warmth exchanger, and vigilant monitoring of stress gauges. These proactive steps make sure the boiler operates inside optimum parameters, minimizing potential issues.
- Common Water High quality Checks: Monitoring water high quality is important to forestall scale buildup and corrosion. Scale buildup reduces warmth switch effectivity, whereas corrosion can injury inside elements. Testing for hardness and different contaminants ensures the water used within the system doesn’t hurt inside elements.
- Thorough Cleansing of the Warmth Exchanger: Common cleansing of the warmth exchanger is essential to forestall buildup of sediment and particles. This buildup reduces warmth switch, rising power consumption and doubtlessly inflicting overheating. Cleansing must be carried out in accordance with producer suggestions.
- Shut Monitoring of Stress Gauges: Common checks of stress gauges are important to make sure the system operates inside secure stress limits. Fluctuations in stress can point out issues corresponding to leaks or air pockets, requiring speedy consideration. Understanding the secure stress ranges to your particular boiler mannequin is paramount.
Inspecting the System for Potential Issues
Common visible inspections of the system are important for figuring out potential issues early on. This consists of checking for leaks, corrosion, and indicators of harm to the warmth exchanger or different elements. This proactive method helps stop main breakdowns and ensures the boiler features effectively.
- Leak Detection: Common inspections ought to embrace thorough checks for any leaks round pipes, joints, and connections. A leak can result in water injury and important power loss. Use soapy water to determine delicate leaks that may not be instantly obvious.
- Corrosion Inspection: Visible inspection ought to embrace a cautious examination for indicators of corrosion on the boiler’s exterior and inside elements. Corrosion can compromise the structural integrity and useful efficiency of the system.
- Warmth Exchanger Situation: Look at the warmth exchanger for any indicators of harm or buildup. Injury to the warmth exchanger can severely influence the boiler’s effectivity. Examine for any cracks, pitting, or different abnormalities.
Optimizing Boiler Effectivity, flush a outdated forged iron fuel boiler system
Optimizing boiler effectivity is essential to minimizing power consumption and decreasing working prices. Correct combustion and airflow are crucial components in maximizing effectivity. Understanding the optimum settings to your boiler mannequin and adjusting as wanted will contribute to improved efficiency.
- Optimum Combustion: Making certain correct combustion of gas is significant for optimum effectivity. Sufficient air provide to the burner and correct gas metering contribute to environment friendly combustion. Changes to the air consumption must be carried out by certified personnel solely.
- Airflow Management: Correct airflow management ensures the boiler operates at peak effectivity. A certified technician can carry out an intensive inspection and needed changes.
Preventative Upkeep Duties
Job | Frequency | Description | Instruments |
---|---|---|---|
Visible Inspection (Leaks, Corrosion) | Month-to-month | Verify for any indicators of leaks, corrosion, or injury to the boiler exterior and inside elements. | Visible Inspection, Screwdrivers, Pliers |
Water High quality Take a look at | Quarterly | Take a look at water for hardness and different contaminants. | Water Testing Equipment |
Warmth Exchanger Cleansing | Yearly | Clear the warmth exchanger to take away sediment and particles. | Specialised Cleansing Options, Brushes, Cleansing Instruments |
Stress Gauge Verify | Weekly | Verify stress gauges to make sure the system operates inside secure limits. | Stress Gauge |
Closing Assessment
Efficiently flushing an outdated forged iron fuel boiler system includes meticulous preparation, adherence to security protocols, and a scientific method to the flushing procedures. By following this complete information, you possibly can restore your boiler’s effectivity and lengthen its lifespan. Bear in mind common upkeep is essential to stopping future issues. Correct post-flush checks make sure the system is operational and free from leaks.
FAQ Part: How To Flush A Previous Solid Iron Gasoline Boiler System
What instruments are wanted for flushing a forged iron boiler?
Instruments wanted might embrace a drain valve wrench, numerous wrenches for disconnections, a stress gauge, and acceptable security gear like gloves and goggles.
How lengthy does it usually take to flush a forged iron fuel boiler?
Flushing time varies primarily based on the scale of the system and the extent of blockages. Anticipate it to take a number of hours, doubtlessly longer for in depth blockages.
What are the indicators that my forged iron boiler wants flushing?
Decreased heating output, uncommon noises, and sluggish water temperature improve are widespread indicators of a boiler needing flushing.
Can I flush a forged iron boiler myself, or ought to I rent knowledgeable?
Whereas this information offers directions, it is advisable to hunt skilled assist should you lack expertise with plumbing or fuel methods. At all times prioritize security.