How one can cease leaking at management valve and riser is an important side of business upkeep. Understanding the basis causes, implementing efficient troubleshooting methods, and adopting preventative upkeep practices are important for minimizing downtime and making certain operational security. This complete information offers an in depth evaluation of the issue, providing insights into figuring out leaks, performing repairs, and in the end stopping future occurrences.
This information delves into the intricacies of management valve and riser leaks, overlaying a variety of crucial features from materials choice to regulatory compliance. It explores numerous potential causes, starting from defective seals to improper set up, and offers sensible troubleshooting strategies for figuring out and isolating the supply of the leak. Moreover, the information offers methods for restore, upkeep, and preventative measures to make sure long-term operational reliability.
Figuring out the Reason behind Leakage
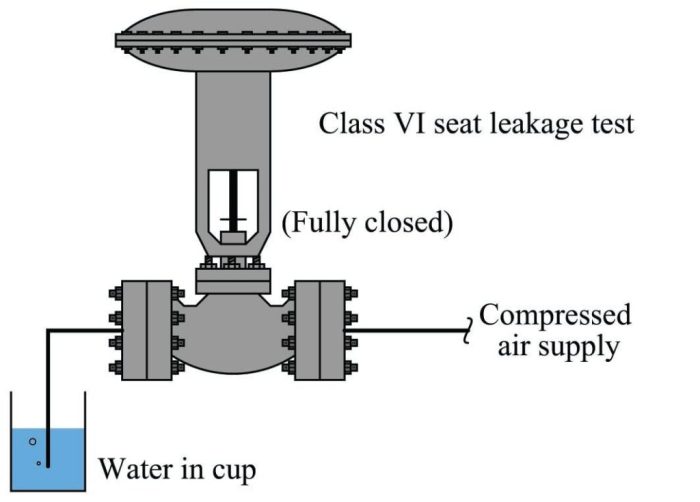
Uncontrolled leakage from management valves and risers can result in important operational points, impacting security, effectivity, and environmental compliance. Understanding the basis causes is paramount to efficient troubleshooting and stopping future incidents. This requires a radical evaluation of potential elements, from defective seals to improper set up practices. A deep dive into the assorted contributing elements will equip us with the data to diagnose and resolve these issues successfully.
Potential Causes of Leakage
Leakage at management valves and risers can stem from a mess of things. These embody points with the valve’s parts, improper set up procedures, or fluctuations in working situations.
- Defective Seals: Management valves rely closely on seals to stop leakage. Broken or deteriorated seals are a typical supply of leakage. Completely different seal sorts exhibit completely different failure modes. Examples embody worn O-rings, broken packing supplies, or improper seal alignment. Improper set up, or repeated cycles of excessive stress, can speed up seal degradation.
- Worn Components: Extended operation and publicity to harsh situations can result in put on and tear on inside valve parts like stems, diaphragms, and valve our bodies. Put on usually manifests as elevated leakage. This could result in expensive upkeep and potential security hazards.
- Improper Set up: Incorrect set up procedures can result in misalignment, improper seating, and different points that contribute to leakage. Elements like inadequate torque throughout set up or incorrect valve positioning may cause leakage.
- Stress Fluctuations: Sudden or important stress adjustments can stress seals and parts, doubtlessly inflicting leakage. Such fluctuations might be brought on by pump points or sudden course of calls for. Sudden stress spikes may cause present minor injury to turn out to be crucial, resulting in leakage.
- Materials Degradation: The supplies used within the building of management valves and risers can degrade over time resulting from publicity to corrosive fluids, excessive temperatures, or different environmental elements. This degradation can weaken the fabric, doubtlessly resulting in leakage. As an example, stainless-steel uncovered to acidic environments might develop pitting corrosion.
- Move Fee Variations: Adjustments within the circulate charge can influence the stresses and forces appearing on the valve parts. Excessive circulate charges can exacerbate present put on, resulting in leakage. Equally, abrupt adjustments in circulate charge can influence sealing parts.
Kinds of Seals and Failure Modes
Management valves make the most of numerous seal sorts, every with distinctive traits and susceptibility to failure.
- O-rings: O-rings are generally utilized in management valves resulting from their simplicity and cost-effectiveness. Nonetheless, they’re vulnerable to compression set and extrusion. Injury may result from improper set up, or extreme stress.
- Packing: Packing supplies are utilized in numerous valve designs to create a seal. Put on, degradation, and improper tensioning are frequent failure modes. The kind of packing materials used is essential for the applying, and the method working situations can have an effect on its lifespan.
- Diaphragms: Diaphragms are employed in some valve designs. Tears, punctures, and materials degradation can result in leakage. Improper mounting or extreme stress can result in these points.
Working Circumstances and Their Affect
Working situations considerably influence the efficiency and longevity of management valves.
- Stress: Excessive working pressures can stress seals and parts, resulting in leakage. The connection between stress and leakage is usually exponential, with leakage rising considerably as stress will increase.
- Temperature: Excessive temperatures can speed up the degradation of seals and different supplies, rising the chance of leakage. Completely different supplies have completely different tolerances for top temperatures.
- Move Fee: Excessive circulate charges can improve the shear and influence forces on the parts, doubtlessly inflicting leakage. Abrupt adjustments in circulate charge can have a detrimental impact on seals and different crucial components.
Management Valve Materials Resistance to Leakage
The selection of fabric for management valves immediately impacts their resistance to leakage.
Materials | Resistance to Leakage | Feedback |
---|---|---|
Carbon Metal | Reasonable | Prone to corrosion in particular environments |
Stainless Metal | Excessive | Gives higher resistance to corrosion and put on |
Alloy Metal | Very Excessive | Wonderful resistance to corrosion and put on, however dearer |
Hastelloy | Wonderful | Extremely proof against corrosion by a variety of chemical compounds |
Supplies choice is crucial in stopping leakage. Elements just like the working setting, temperature, and stress want cautious consideration.
Troubleshooting Strategies
The guts-wrenching expertise of a leaking management valve or riser calls for a methodical and exact strategy. We should transfer past the preliminary shock and concern of the unknown to systematically diagnose the supply of the leak and implement swift, efficient options. A measured, step-by-step strategy is essential to stopping additional injury and expensive repairs. Understanding the supply and severity of the leak is the primary crucial step in making certain the security and performance of your complete system.A radical inspection is not only a activity; it is a meticulous course of demanding unwavering consideration to element.
This proactive strategy is essential for not solely containing the leak but additionally stopping doubtlessly catastrophic penalties, comparable to additional injury or harmful stress fluctuations. Each step, from visible assessments to superior leak detection strategies, contributes to a complete understanding of the issue.
Systematic Inspection Procedures
A methodical strategy to inspecting management valves and risers is important. Start with a visible examination, meticulously scrutinizing each joint, becoming, and connection. Search for any indicators of corrosion, put on, or deformation. Pay explicit consideration to areas recognized to be inclined to emphasize or pressure. Subsequent, rigorously test for any indicators of leakage, together with drips, puddles, or seen streams.
Doc these observations meticulously. If potential, think about using specialised instruments like borescopes for deeper examination of hard-to-reach areas.
Assessing Leakage Severity
Correct evaluation of the leakage severity is crucial for efficient containment and restore. Visible inspection offers a preliminary evaluation, however extra definitive strategies are sometimes required. Stress testing entails rigorously making use of managed stress to the system whereas monitoring for leaks. This enables for exact identification of the leak’s location and severity. Specialised leak detection strategies, comparable to dye penetrants or acoustic emission, can pinpoint even minute leaks that could be missed by visible inspection.
Every methodology presents a singular perspective, enabling a complete understanding of the issue’s scale.
Isolation of the Affected Part
Swift isolation of the affected part is paramount to containing the leakage and stopping additional injury. This usually entails shutting down valves strategically to limit the circulate of fluids. Fastidiously take into account the potential influence on different components of the system, and meticulously observe security protocols to stop unintended penalties. The aim is to isolate the supply of the leak, permitting for managed restore with out jeopardizing the security of personnel or gear.
Security should all the time be the highest precedence.
Mandatory Instruments and Gear
Class | Device/Gear | Description |
---|---|---|
Visible Inspection | Borescope, Flashlight, Magnifying Glass | Important for inspecting hard-to-reach areas and detecting delicate indicators of injury or leakage. |
Stress Testing | Stress Gauge, Stress Pump, Valves | Permits exact identification of leak location and severity. |
Leak Detection | Dye Penetrant Equipment, Acoustic Emission Detector | Pinpoints minute leaks missed by visible inspection. |
Isolation | Valves, Shut-off mechanisms | Essential for holding the leak and stopping additional injury. |
Security | Security Glasses, Gloves, Private Protecting Gear | Important for making certain the security of personnel through the troubleshooting course of. |
Restore and Upkeep Methods
A heart-wrenching expertise arises when a management valve or riser leaks. It is not only a mechanical downside; it is a potential menace to effectivity, security, and profitability. Addressing these leaks calls for a proactive strategy, shifting past merely fixing the fast difficulty and delving into preventative upkeep. The next methods supply a roadmap to long-term success, making certain your techniques stay sturdy and dependable.
Restore Choices for Leakage Issues
Completely different leakage situations necessitate tailor-made restore approaches. Understanding the basis trigger is essential to choosing the best answer. Listed below are a number of potential restore choices:
- Seal Alternative: Broken seals are a typical wrongdoer. Changing worn-out seals with high-quality, appropriate replacements is usually the best answer. This ensures a decent, leak-free seal, stopping additional injury and expensive downtime. For instance, a defective packing gland in a pneumatic management valve may have a whole substitute, making certain no air escapes via the gland.
- Valve Changes: In some instances, minor changes to valve settings can resolve leaks. Calibration and fine-tuning of valve parameters can restore correct operation and eradicate leaks. This can be a cost-effective strategy if the issue is linked to improper valve positioning or stress settings. Exact changes to the valve stem and packing can restore its sealing capabilities.
- Element Restore: If a particular valve part is broken, such because the actuator or physique, restore or substitute could also be mandatory. A broken actuator may require specialised restore or substitute to make sure clean operation and forestall future leaks. Cautious examination of the affected half is crucial to find out the extent of the injury and the most effective restore technique.
- Riser Inspection and Restore: Leaking risers usually level to corroded or broken sections. Thorough inspection of the riser, together with visible checks and stress testing, is crucial to pinpoint the precise location of the injury. Restore choices embody welding, patching, or changing corroded sections, making certain the integrity of the riser is restored. As an example, a crack in a riser pipe might necessitate welding to stop additional leaks and potential security hazards.
Greatest Practices for Sustaining Management Valves and Risers
Proactive upkeep is paramount to stopping leaks. Implementing a complete upkeep schedule, together with common inspections and preventative measures, considerably reduces the chance of future issues. It’s an funding in security, effectivity, and long-term price financial savings.
- Common Inspections: Visible inspections of valves and risers, coupled with periodic stress testing, are important to detect potential points early. This enables for well timed intervention, stopping small issues from escalating into main leaks and expensive repairs. Common checks for corrosion, put on, and misalignment are very important in stopping future points.
- Correct Lubrication: Sustaining correct lubrication of shifting components, like valve stems, reduces friction and put on, extending the lifespan of the parts. Constant lubrication minimizes the chance of leaks resulting from mechanical put on and tear. This proactive strategy minimizes the necessity for emergency repairs.
- Cleansing and Flushing: Common cleansing and flushing of the system can take away particles and contaminants that may contribute to corrosion and leakage. That is particularly essential in harsh environments the place contaminants are prevalent. This important step is an funding within the integrity of the system.
- Documentation and Information: Sustaining detailed information of upkeep actions, together with dates, procedures, and findings, is crucial for future troubleshooting and planning. This complete documentation ensures that mandatory upkeep is carried out and that any points are promptly recognized and resolved.
Significance of Common Upkeep Schedules
Common upkeep schedules are very important for minimizing leakage frequency and making certain the longevity of your management valves and risers. Constant upkeep reduces sudden downtime and prevents important monetary losses related to expensive repairs.
“Proactive upkeep is considerably more cost effective than reactive upkeep, the place points are addressed solely after they’ve escalated.”
Upkeep Procedures for Numerous Valve Varieties
A tailor-made upkeep strategy is crucial for various valve sorts. This desk Artikels the precise procedures for numerous management valve sorts:
Valve Kind | Inspection Procedures | Upkeep Procedures |
---|---|---|
Pneumatic Valves | Test for leaks in pneumatic strains, examine actuators for injury | Lubricate actuators, exchange seals if mandatory |
Electrical Valves | Examine wiring, test motor operation | Clear contacts, lubricate shifting components |
Diaphragm Valves | Examine diaphragm for injury, test seals | Substitute broken diaphragms, guarantee correct seating |
Globe Valves | Test for leaks within the physique, examine stem for put on | Substitute worn components, lubricate stem |
Stopping Future Leaks
A continuing concern hangs over each operation, the specter of leaks. However prevention is not nearly stopping the drips; it is about constructing a system the place leaks are anomalies, not the norm. This important step entails a shift in perspective, shifting from reactive fixes to proactive design and upkeep. By understanding the basis causes and using sensible methods, we will forge a future the place leaks are minimized, operations run easily, and everybody can breathe a collective sigh of reduction.
Design Concerns for Management Valves and Risers, How one can cease leaking at management valve and riser
The design of management valves and risers immediately impacts their susceptibility to leaks. Cautious consideration of supplies, tolerances, and stress rankings is paramount. Using high-quality, corrosion-resistant supplies within the valve our bodies and riser piping is essential to face up to the trials of operation. Precision in manufacturing and meeting reduces stress factors, thus minimizing the chance of fatigue-induced cracking, a frequent wrongdoer in long-term leaks.
Thorough stress evaluation through the design section may help establish and mitigate potential weak factors.
Significance of Correct Set up Procedures
Set up errors are a frequent supply of leaks, a silent menace lurking inside seemingly good techniques. Correct set up procedures, meticulously adopted, are very important for a leak-free operation. A misaligned valve, improperly tightened connections, or insufficient help for the riser can all result in leaks that escalate over time. Coaching personnel on correct set up strategies, utilizing the right instruments, and adhering to established protocols are important safeguards.
Using leak detection gear throughout set up can catch points early, saving time and stopping main issues down the road. Moreover, rigorous high quality checks and common inspections all through the set up course of must be enforced to take care of excessive requirements.
Preventative Upkeep Methods
Proactive upkeep is the cornerstone of leak prevention. Common inspections, well timed upkeep checks, and diligent monitoring of crucial parts can considerably scale back the chance of future incidents. This consists of checking for corrosion, verifying correct valve operation, and monitoring stress fluctuations within the riser system. Utilizing specialised instruments and gear for leak detection can establish potential points early on.
Common lubrication and changes of shifting components in management valves can considerably lengthen their lifespan and forestall untimely put on, a typical reason behind leakage.
Management Valve Designs and Leakage Prevention Options
Valve Design | Leakage Prevention Options | Instance Utility |
---|---|---|
Ball Valve | Easy design, usually with double seals and high-quality sealing supplies; available for numerous sizes and pressures. | Normal function management purposes |
Globe Valve | Exact management over circulate charges; numerous seat designs for various fluid viscosities and pressures. | Functions requiring exact circulate regulation |
Butterfly Valve | Compact design, appropriate for high-flow purposes; usually used with resilient seals. | Giant-diameter pipelines, high-flow management |
Diaphragm Valve | Seals with resilient diaphragms, good for corrosive fluids and purposes requiring low upkeep; sometimes utilized in chemical processes. | Chemical processing, corrosive liquids |
Every design has distinctive benefits and drawbacks in stopping leakage, so your best option is dependent upon the precise software. Understanding these options is essential to choosing the suitable valve for a given course of and minimizing the chance of leaks.
Case Research and Examples
A relentless battle towards leaks, whether or not in management valves or risers, usually checks the resilience of engineering groups. These leaks aren’t simply inconvenient; they symbolize a cascade of potential issues, from manufacturing downtime and expensive repairs to security hazards and environmental injury. Understanding previous struggles and triumphs in mitigating these points is essential to growing proactive and efficient methods for the longer term.
Let’s delve into some real-world situations.The frustration of coping with a persistent leak, the hours spent on diagnostics, and the reduction of lastly discovering an answer are all a part of the human expertise in engineering. These case research illuminate the various challenges and showcase profitable methods for stopping these unwelcome occurrences. The detailed evaluation of those real-world conditions offers invaluable classes for implementing efficient preventative measures.
Case Research 1: The Corroded Management Valve
A chemical processing plant skilled a recurring leak in a management valve chargeable for regulating stress within the reactor. Preliminary troubleshooting revealed important corrosion within the valve’s physique, brought on by the aggressive nature of the method fluid. The corrosion had weakened the valve’s construction, resulting in a gradual improve in leakage over time. The answer concerned changing the corroded valve with a extra resistant materials, comparable to a high-nickel alloy, and implementing a extra rigorous upkeep schedule that included common inspection and cleansing of the valve.
The plant additionally switched to a much less corrosive fluid, the place potential, lowering the chance of future corrosion.
Case Research 2: The Riser System Failure
An influence plant skilled a major leak in a riser pipe used for transporting high-pressure steam. The leak originated from a stress-induced crack within the riser’s weld. The troubleshooting concerned meticulous examination of the weld joints, materials evaluation, and stress testing to establish the basis trigger. The restore concerned a complete weld restore process, adopted by a radical stress check to make sure the integrity of the repaired part.
Subsequent monitoring and a refined inspection schedule prevented additional issues. A key takeaway from this case research was the significance of stringent weld high quality management and common inspection of crucial parts.
Case Research 3: The Valve Stem Sticking
A water therapy plant encountered a valve stem sticking difficulty, resulting in intermittent leakage from the management valve. The evaluation confirmed that the valve stem was accumulating deposits over time, lowering lubrication and inflicting friction. The answer concerned implementing a preventative upkeep technique that included periodic valve stem lubrication and cleansing. In addition they examined the method parameters to establish any elements that may contribute to the buildup of deposits.
As well as, the plant investigated different lubrication strategies, which proved to be an efficient technique for stopping future stem sticking and leaks.
Prevention Methods and Analysis
A profitable leak prevention technique depends on a multi-faceted strategy, combining proactive upkeep with rigorous inspection and monitoring. In all three case research, the effectiveness of the carried out prevention methods was evaluated via common monitoring of the affected parts. The information collected was used to fine-tune the upkeep schedule and establish any rising traits or potential dangers. A complete strategy is crucial to stopping leaks.
Key Learnings and Greatest Practices
Case Research | Root Trigger | Troubleshooting | Restore/Resolution | Prevention Technique |
---|---|---|---|---|
Corroded Management Valve | Aggressive course of fluid | Corrosion inspection | Materials substitute, improved upkeep | Materials choice, common inspection |
Riser System Failure | Stress-induced crack in weld | Weld examination, stress testing | Weld restore, stress testing | Stringent weld high quality management, common inspections |
Valve Stem Sticking | Deposit accumulation, diminished lubrication | Valve stem lubrication, course of parameter evaluation | Periodic lubrication, course of changes | Preventative upkeep, lubrication optimization |
These case research spotlight the crucial significance of a proactive and data-driven strategy to leak prevention. A complete analysis of potential causes, coupled with acceptable troubleshooting and restore methods, is essential for minimizing downtime and making certain security.
Materials Choice and Compatibility: How To Cease Leaking At Management Valve And Riser
Choosing the proper supplies for management valves and risers is not only about selecting one thing that appears robust; it is about making certain the long-term well being and security of your complete system. A fabric incompatible with the method fluid can result in catastrophic failures, inflicting not solely expensive repairs but additionally potential environmental injury and security hazards. This cautious choice is paramount for sustaining a dependable and environment friendly operation.Choosing supplies appropriate with the method fluid and working situations is crucial to stop leakage.
A mismatch between materials and setting can set off corrosion, erosion, or different degradation processes, in the end resulting in leaks and failures. This delicate stability between materials properties and the method setting immediately impacts the system’s lifespan and total efficiency.
Elements Influencing Materials Choice
Materials choice for management valves and risers hinges on a number of crucial elements. Corrosion resistance, a cloth’s capability to face up to the corrosive results of the method fluid, is paramount. Temperature tolerance is one other key consideration, as excessive temperatures may cause supplies to weaken or change their properties over time. The working stress and the anticipated service lifetime of the gear additionally play an important position in materials selection.
Moreover, cost-effectiveness and availability are additionally important elements within the decision-making course of.
Lengthy-Time period Efficiency and Stability
The long-term efficiency and stability of a cloth are immediately associated to its resistance to degradation. Over time, supplies can expertise stress cracking, pitting, or different types of injury resulting from elements like corrosion, erosion, or fatigue. The precise working situations, together with temperature fluctuations, stress variations, and publicity to aggressive chemical compounds, tremendously influence the fabric’s longevity. Understanding the long-term stability of various supplies within the particular setting is essential for stopping expensive failures and downtime.
For instance, stainless steels are recognized for his or her corrosion resistance in lots of environments, however their efficiency in high-temperature, high-pressure purposes may require specialised alloys.
Comparability of Materials Properties
The desk under illustrates the properties of varied supplies appropriate for management valves and risers. It is essential to match the fabric’s properties to the precise necessities of the method setting to make sure optimum efficiency and longevity.
Materials | Corrosion Resistance | Temperature Tolerance (°C) | Power | Price |
---|---|---|---|---|
Carbon Metal | Reasonable | As much as 450 | Good | Low |
Stainless Metal (316L) | Wonderful | As much as 800 | Good | Medium |
Hastelloy C-276 | Wonderful (aggressive chemical compounds) | As much as 650 | Excessive | Excessive |
Monel | Wonderful (sea water, some acids) | As much as 650 | Excessive | Medium-Excessive |
Nickel-Based mostly Alloys | Wonderful (extremely corrosive environments) | As much as 1100 | Excessive | Excessive |
Regulatory Compliance and Security
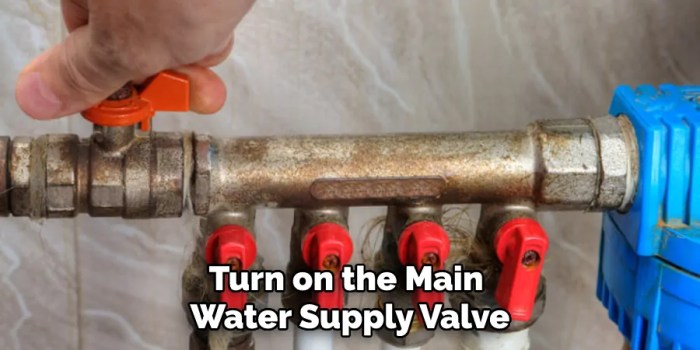
A way of profound duty hangs heavy over the prevention of leaks in management valves and risers. These techniques, very important to numerous operations, demand unwavering adherence to security protocols and laws. Failing to satisfy these requirements can have devastating penalties, not simply financially, but additionally by way of human life and environmental influence. Understanding and meticulously implementing regulatory compliance is paramount for safeguarding lives and defending our planet.A radical grasp of security laws is not only a matter of ticking containers; it is about constructing a tradition of security that permeates each side of operation, inspection, and upkeep.
This proactive strategy prevents accidents, minimizes potential hurt, and instills a deep sense of safety in those that depend on these crucial techniques.
Regulatory Necessities for Leakage Prevention
Compliance with regulatory necessities is crucial for making certain the protected and dependable operation of management valves and risers. These laws usually dictate particular design requirements, materials specs, and operational procedures to mitigate the dangers related to leaks. This ensures that each side of the system is constructed with security as its cornerstone.
Security Protocols Throughout Inspection, Restore, and Upkeep
Safeguarding personnel throughout inspection, restore, and upkeep is paramount. A complete set of security protocols have to be rigorously adopted. These protocols ought to embody private protecting gear (PPE), confined area entry procedures, and lockout/tagout protocols to stop unintentional publicity to hazardous situations.
Significance of Emergency Response Plans for Leakage Incidents
Preparedness for leakage incidents is essential. A well-defined emergency response plan, incorporating communication protocols, evacuation procedures, and the deployment of acceptable sources, is crucial for minimizing the influence of any leakage incident. A swift and arranged response is important to containing the injury and safeguarding these concerned.
Desk of Related Security Rules
The desk under Artikels key security laws and their applicability throughout completely different industries. Understanding these laws and their particular necessities inside every business is essential for acceptable compliance.
Security Regulation | Description | Applicability |
---|---|---|
OSHA (Occupational Security and Well being Administration) | Complete set of requirements for employee security and well being in the USA. | Big selection of industries, together with oil & gasoline, manufacturing, and building. |
API (American Petroleum Institute) | Requirements particularly for the oil and gasoline business, overlaying gear design, operation, and upkeep. | Oil and gasoline manufacturing, refining, and transportation. |
EPA (Environmental Safety Company) | Rules centered on environmental safety, together with controlling emissions and dangerous substance releases. | Industries that deal with hazardous supplies, together with chemical processing and manufacturing. |
NFPA (Nationwide Hearth Safety Affiliation) | Requirements addressing hearth security and prevention, together with the dealing with of flammable and flamable supplies. | Industries dealing with flammable supplies, together with chemical vegetation and storage amenities. |
Ultimate Conclusion
In conclusion, successfully managing management valve and riser leaks requires a multi-faceted strategy encompassing thorough inspection, systematic troubleshooting, and proactive upkeep. By understanding the basis causes, implementing acceptable restore methods, and adopting preventative measures, industries can decrease downtime, guarantee security, and improve the general operational effectivity of their techniques. This information presents a complete roadmap for attaining these objectives.
Person Queries
What are frequent causes of management valve leaks in addition to defective seals?
Improper set up, worn components, stress fluctuations, and incompatible supplies may result in leaks. Working situations comparable to temperature and circulate charge may affect the chance of leakage.
What instruments are mandatory for troubleshooting valve and riser leaks?
Instruments wanted for troubleshooting might fluctuate based mostly on the severity and nature of the leak, however sometimes embody visible inspection instruments, stress gauges, leak detection gear, and doubtlessly specialised wrenches and dismantling instruments.
What are some preventative upkeep methods to cut back leakage incidents?
Common upkeep schedules, correct set up procedures, and utilizing appropriate supplies for the precise software are key methods to stop leaks. Design issues for valves and risers must also issue within the potential for leaks.
How do regulatory necessities have an effect on leakage prevention?
Particular industries and areas have laws concerning leakage prevention. Following security protocols throughout inspection, restore, and upkeep is essential, in addition to having emergency response plans in place.